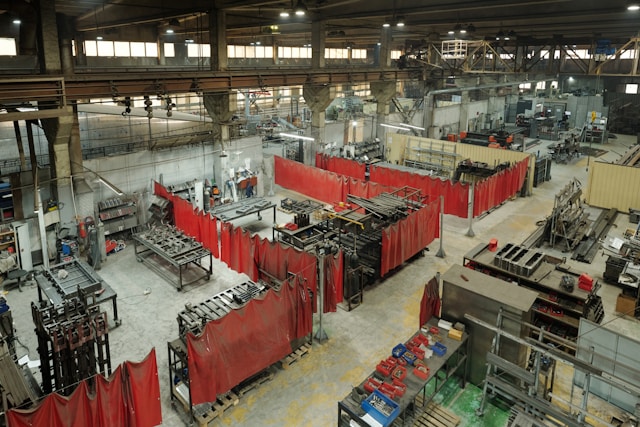
Industrial site operations are the backbone of many production-driven industries. The efficiency of these operations directly affects a company’s bottom line, safety standards, and environmental impact. Optimizing these operations as industries continue to evolve has become even more critical. This article will explore the components of effective industrial site management, best practices to maximize efficiency, the growing role of technology, and how sustainable practices contribute to long-term success.
Key Factors that Influence Industrial Site Operations
Industrial site operations involve various interconnected factors that must be carefully managed to ensure smooth functioning. One of the key elements is manufacturing processes, which serve as the core of operations. The efficiency of these processes, from the arrival of raw materials to the production of finished goods, can significantly impact productivity. A streamlined production system ensures that goods are produced on time, with minimal waste, and at high quality. Companies that invest in process optimization, such as lean manufacturing techniques, often see improved throughput and reduced operational costs.
Logistics is another critical factor influencing industrial site operations. Managing the flow of materials, components, and finished products efficiently ensures that the production line remains uninterrupted. Poor logistics can lead to delays, missed deadlines, and a ripple effect of inefficiency throughout the entire operation. Advanced inventory systems, supply chain coordination, and just-in-time inventory management are essential for keeping operations smooth and cost-effective.
Another significant component is equipment management. Industrial machinery is subject to wear and tear over time, and without a proper maintenance plan, it can cause downtime that disrupts production schedules. An effective asset management strategy involves preventative maintenance, real-time monitoring of equipment conditions, and swift interventions to prevent equipment failures. This proactive approach helps ensure that machinery operates at peak performance and reduces costly breakdowns.
Safety and compliance also play a significant role in the overall efficiency of industrial operations. A well-maintained safety system minimizes the risks of accidents and injuries, fostering a healthier, more productive work environment. Industrial sites are subject to various regulations, from environmental standards to workplace safety protocols. Meeting these standards is essential for legal compliance, protecting workers, and maintaining a company’s reputation.
Effective Best Practices for Streamlining Operations
To improve industrial site efficiency, it’s essential to implement best practices that continuously streamline operations and reduce waste. One such practice is lean manufacturing, which aims to eliminate unnecessary steps and reduce inefficiencies in the production process. Techniques like Six Sigma, Total Productive Maintenance (TPM), and Kaizen focus on continual improvement by identifying inefficiencies, reducing defects, and optimizing workflow. These strategies ensure that resources are used effectively, minimize production costs, and maximize operational output.
Employee training and development are also critical to improving operational efficiency. A well-trained workforce is more likely to work at a higher level of productivity, with fewer errors, faster issue resolution, and greater safety awareness. Providing employees with the necessary training to handle new technologies, safety standards, and operational strategies ensures that they can perform their duties effectively and with confidence. Investing in the skills of workers not only improves overall site performance and contributes to job satisfaction and lower turnover rates.
Energy efficiency is another key focus for industries striving to optimize their operations. Many industrial sites consume vast amounts of energy, making energy management a crucial aspect of cost-saving and environmental impact reduction. Implementing energy-efficient practices, such as upgrading to energy-saving equipment, optimizing heating and cooling systems, and improving lighting, can lead to significant savings. Additionally, businesses are increasingly exploring renewable energy sources, such as solar or wind power, to reduce reliance on nonrenewable energy and lower operational costs.
Automation is transforming industrial operations by streamlining repetitive tasks, reducing the need for manual labor, and enhancing overall efficiency. Industries can increase production speed and precision by integrating robotics and automated material handling systems while minimizing human error. Automation is particularly beneficial in assembly, packaging, and material transportation, allowing human resources to focus on more complex tasks that require problem-solving and decision-making.
Lastly, leveraging data and analytics is becoming an essential best practice. Collecting real-time data from equipment, inventory systems, and production lines allows managers to monitor operations and identify areas for improvement. Predictive analytics, for example, can help anticipate equipment breakdowns or predict shifts in market demand. By making data-driven decisions, industrial sites can adapt quickly to changes and ensure smoother, more efficient operations.
Leveraging Technology for Greater Productivity
Technology has become a driving force behind the efficiency of industrial operations. As industrial sites become more complex and interconnected, digital tools and systems are proving to be invaluable assets. One such technology is the Internet of Things (IoT), which allows machines, equipment, and tools to communicate with each other and with operators in real time. IoT devices can monitor temperature, pressure, and other key metrics, alerting operators to any potential issues before they cause significant disruptions. Industrial sites can improve predictive maintenance and minimize unplanned downtime by integrating IoT into operations.
Artificial intelligence (AI) and machine learning (ML) are also changing how industries optimize their operations. By analyzing large datasets, AI algorithms can identify patterns and insights that human operators might overlook. For example, AI can predict machine failures, optimize supply chain management, or improve production schedules. Machine learning models can continuously improve based on new data, enhancing the site’s ability to operate efficiently.
Robotics and automation technologies are revolutionizing industrial production by performing repetitive, labor-intensive tasks with high precision and speed. Robotics can be used for assembly, welding, packaging, and material handling, which are essential for maintaining efficient production workflows. Integrating robotics reduces human error, increases throughput, and creates a safer working environment by handling dangerous tasks.
Cloud computing is another technology that has greatly impacted industrial site operations. By utilizing cloud-based platforms, data can be stored and accessed in real time, allowing for better collaboration and decision-making. Cloud computing also facilitates the integration of various technologies, providing a unified approach to managing industrial operations. This system offers scalability, enabling industrial sites to adjust to fluctuations in demand without heavy infrastructure investments.
Sustainable Approaches for Future-Proof Operations
Sustainability has become a key focus for industrial operations as businesses aim to reduce their environmental impact and contribute to long-term ecological goals. Adopting sustainable practices improves a company’s reputation and offers financial benefits. One of the primary areas where sustainability can be integrated into industrial operations is waste reduction and recycling. By reducing waste generation and reusing materials wherever possible, industrial sites can minimize their environmental footprint and reduce disposal costs. Recycling programs can also ensure that valuable materials are reused rather than discarded.
Green manufacturing processes are also a critical component of sustainable industrial operations. These processes focus on minimizing resource consumption, reducing emissions, and using eco-friendly materials. Companies can adopt cleaner energy sources, such as wind or solar power, and implement energy-efficient technologies to reduce their carbon footprint. These efforts benefit the environment and can result in cost savings over time, as renewable energy sources often have lower long-term operational costs than fossil fuels.
Water conservation is another important aspect of sustainability for industrial sites. Water is an essential resource in many industrial processes, but it is also increasingly scarce in some regions. Water-saving measures, such as water recycling and the efficient management of water resources, can significantly reduce water usage and lower operational costs. Some industries have even adopted closed-loop water systems, which help minimize waste and ensure water is used as efficiently.
Lastly, reducing carbon emissions is a key priority for many industries looking to create sustainable operations. By adopting energy-efficient machinery, reducing waste, and using renewable energy sources, companies can significantly lower their carbon footprint and contribute to environmental sustainability. These practices meet regulatory requirements and align with consumer expectations and industry standards.
Optimizing industrial site operations is crucial for enhancing productivity, reducing costs, and ensuring long-term success. Businesses can streamline their operations and improve efficiency by focusing on key factors like manufacturing processes, logistics, and equipment management. Leveraging technology such as IoT, AI, and automation can also provide significant advantages, while sustainable practices help future-proof operations for a greener, more cost-effective future. As industries evolve, adopting a holistic approach to operational optimization will be key to staying competitive in an ever-changing market.